The Excess Instrument Problem
In an earlier post, we demonstrated the power of data-driven instrument tray rationalization through OpFlow. For just two tray types, OpFlow was able to remove over 1,200 instruments from circulation for that hospital.
Repeating that same process for a hospital’s 30 to 40 highest priority instrument trays may yield an excess of 15,000 to 20,000 instruments that the hospital can now re-allocate for other purposes.
The immediate benefit of instrument tray rationalization relates to the cost savings achieved through processing fewer instruments unnecessarily, thereby improving the quality and efficiency of sterile processing and reducing in-room set-up times.
Additionally, those unused instruments no longer incur the inherent depreciation that results with each processing cycle, which reduces the need for repair, and extends the life of the instrument.
<img src="https://images.squarespace-cdn.com/content/v1/5a7cf6304c0dbf7eb12ca0bf/1566231277276-89JR16FFREZLU1KCBIZC/Instruments+removed+from+13+Vascular+Trays.jpg" alt="Instruments removed from 13 Vascular Trays.jpg" />
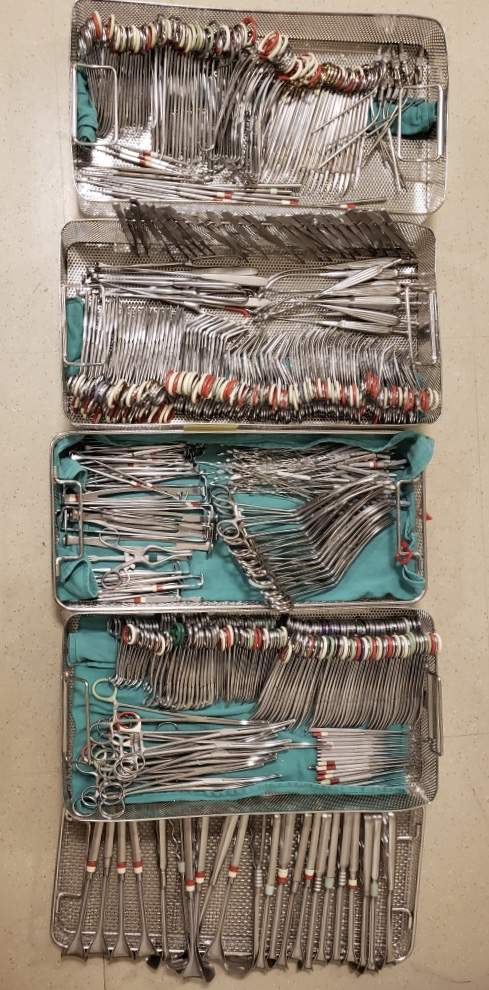
But even more striking are the opportunities that exist for utilizing that instrument surplus:
Hospitals are able to replace (rather than re-purchase) damaged or missing instruments, using their own inventory comprised of the instruments that were removed from those trays.
Hospital systems are able to redistribute excess instrumentation to other hospitals in the system, avoiding the need for new purchases.
Hospitals that are exploring options for off-site instrument reprocessing due to logistical constraints on-site are able to do so with greater ease through utilization of the surplus instruments.
Finally, any remaining instruments may also serve as an opportunity for a charitable contribution for the hospital.
By applying data-driven lean methodology to the process of instrument tray rationalization, the OpFlow analytics platform delivers immediate and on-going value for hospitals.